Category
Ex nihilo (from nothing)
Make an item from the very beginning, starting with raw materials
Entrant
Melissa Wijffels
Entry
Burnished blackware pottery
Having learned that most pottery in medieval Europe and beyond was unglazed earthenware, and that it was not only possible, but common early period for earthenware to be fired in a hearth fire rather than a kiln, I decided to make some pottery from first principals.
The process, in brief, was as follows:
- The clay was dug from a local site and carried back home
- The wet clay clods were then dried until bone dry
- When completely dry, the clay was mixed with water and allowed to rehydrate. Rehydrating when completely dry results in the clay hunks breaking down into a clay slurry, whereas adding water to partially wet native clay results in gooey lumps in solution even months later The clay water was then thuroughly mixed and, after about 5 seconds, poured off into a separate vessel through a screen, leaving behind stones and coarse sand in the bucket, and roots and other organic material in the screen
- A splash of vinegar was added to the 10L mixture as a deflocculant, decreasing settling time for this clay from weeks to days
- After ~4 days, the water was decanted, and the clay slurry dried by hanging in a cloth bag.
- When dry to the consistancy of good working clay, the bag was removed from its hook, and the clay wedged on the cloth. If the centre was still too sticky, the clay was patted flat and folded in the cloth and left in a sunny, sheltered location
- For each pot, I removed a wadge of clay and added ~20% temper (finely crushed pottery shards), as this ratio has been identified in the academic literature as well as by experimental archaeologists as a good starting ratio to reduce the chance of pots exploding when fired
- Following post-Roman practice across much of Europe (the collapse of industrial production of Roman pottery resulting in many places to the loss of the technology of the potters wheel), I coil-built some pots, using thick coils >2cm in diameter, following the meta-structure from archaeological finds and joined each coil before adding the next
- Coils were blended together with my hands as well as a gourd scraper (more commonly used in the Americas where such gourds are native). For future projects, I will carve a wooden scraper, as this type of tool is common in historical pottery traditions from western Europe through to east Asia
- I worked the pot on a board on my lap, turning it manually. When finished, I covered the board with a cloth to allow it to slowly dry to avoid cracking.
- When the pot was leather hard, I burnished it with a smooth stone
- I then left the pot to dry for 2-4 weeks, or until no longer cool when touched to the cheek
- On the day of firing, I preheated the pots for 1-2 hours to remove the chemically bound water from the clay body
- I built a wood fire in our braai, burned the first set of branches to coals while warming pots around the fire, turning frequently. Sandstone pieces were also left near the fire to heat and release moisture so they could be used as kiln furniture
- Once the primary fire burned to coals, I put the kiln furniture on the coals, and then stacked the pottery on top of them
- I then built a teepee of new firewood on top of the previous coals and pottery, trying my best to get the fire going evenly around the entire circumfrence (not easy!)
- Pottery will be fired to earthenware if you can see it glowing cherry red or orange through the firewood
- Once the fuel burned down with gap between pieces (15-30 minutes), I removed the remaining firewood and coals away from the pottery, topped the hot pots with hay, which nearly instantly ignited, and smothered it with a bucket. The smoke from the hay imparts carbon into the polished
surface of the pottery - When fully cool, several hours later, the bucket can be removed and the finished pots examined
Between Nathanael and myself, we dug up and processed the clay, fossicked the sandstone, made the pottery, cut the wood, and sicled and dried the hay, all with hand tools. The braai was the principal anachronism, but fire containment was necessary to do this in an urban area.
Overall, there have been some successes (and some disasters!), but unlike a pottery class or collective, all
of the materials and equipment can be obtained (potentially!) for free, so the barrier to entry is low, and it
felt safe to ‘have a go’. I hope some others try this as well, it’s good fun!
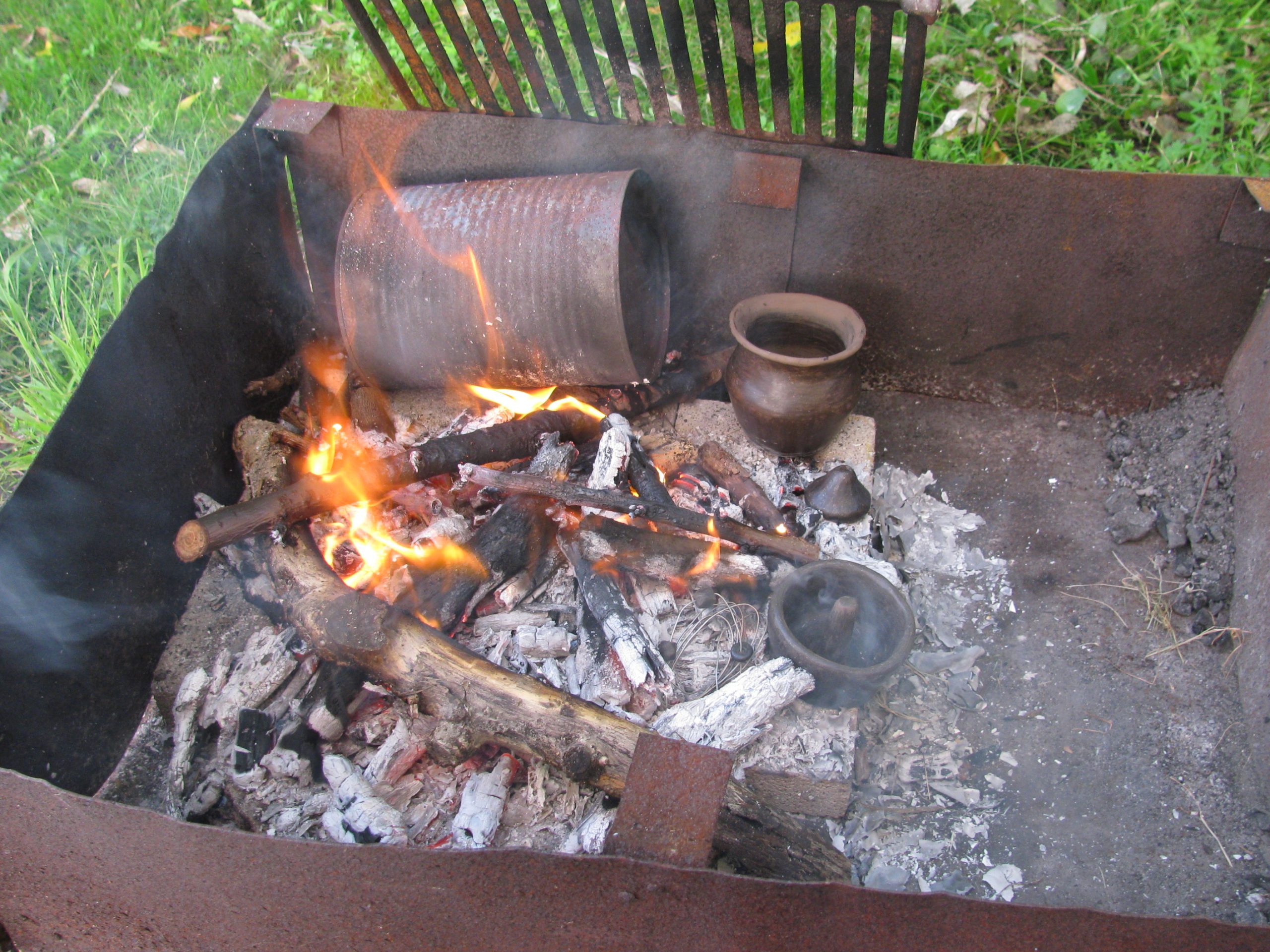
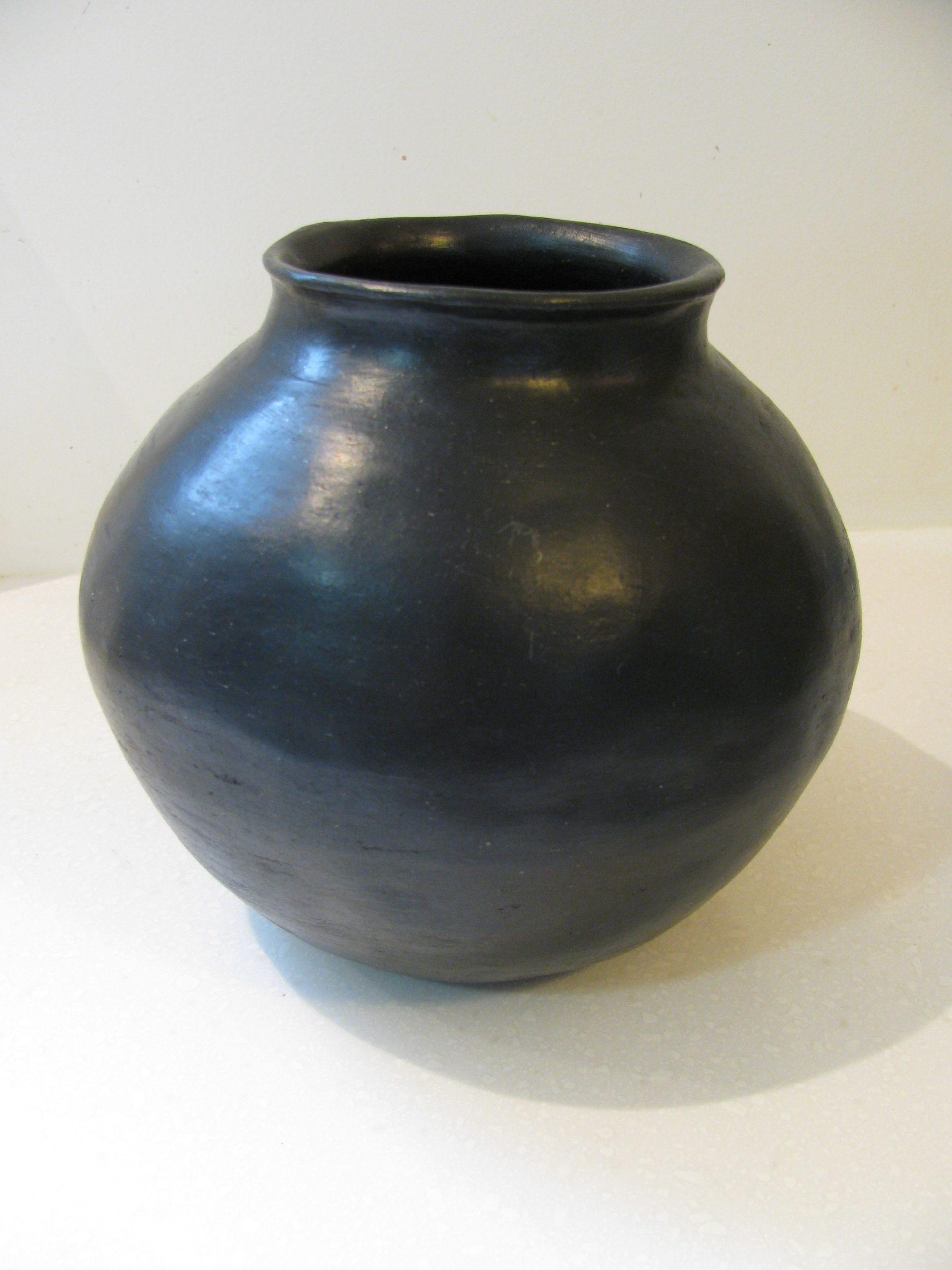
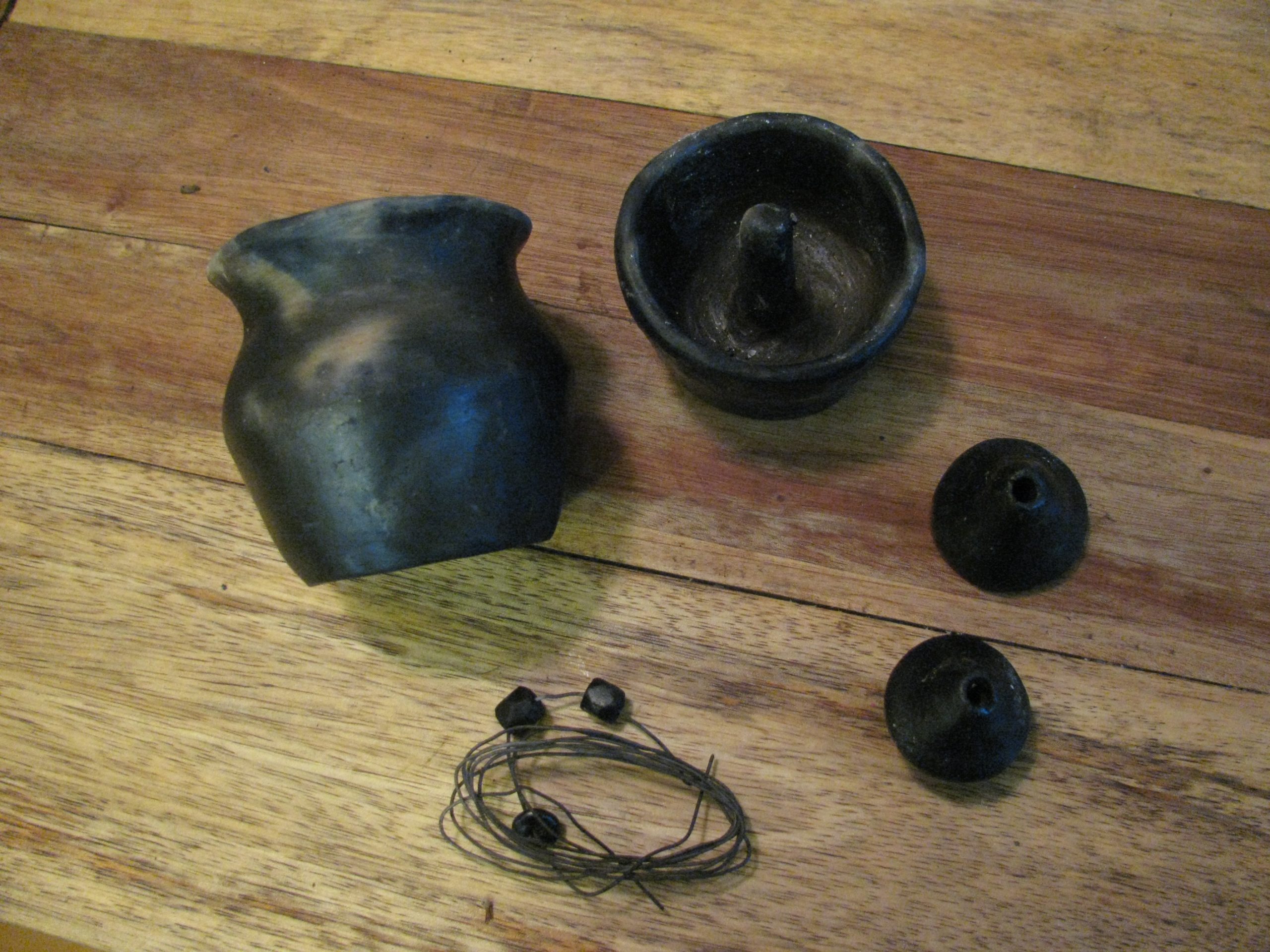
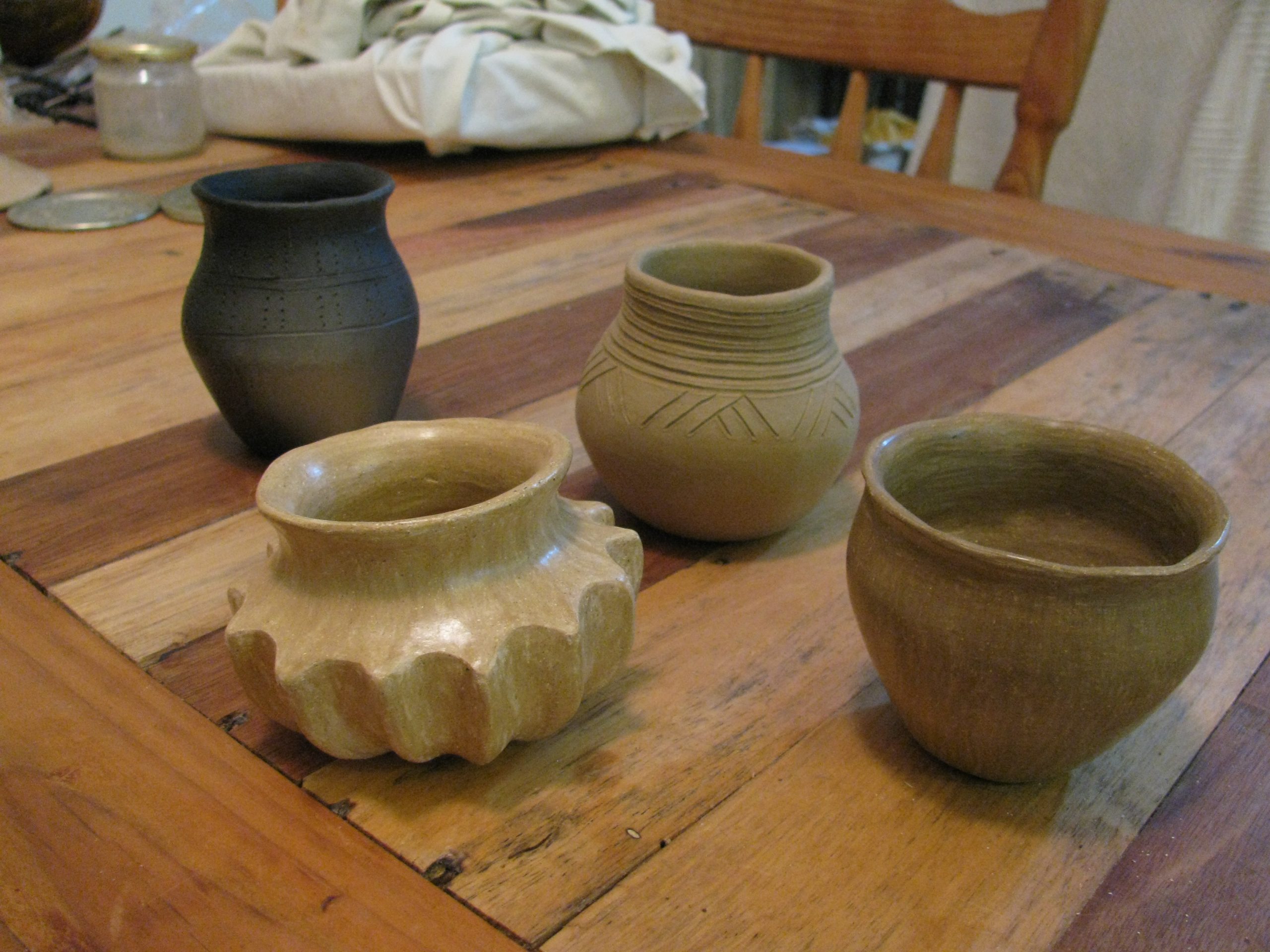